
FORGED CARBON, ALLOY & TOOL STEEL
IMAGE OF 434 @ 200X GENERATED IN-HOUSE
.jpg)
High Strength & Toughness
Forged carbon, alloy and tool steels are used for applications in almost every industry due to their unique properties and versatility.
CARBON STEEL
Low-cost carbon steel grades are commonly used for applications without high strength or operating in high-temperature environments.
ALLOY STEEL
Alloy steel uses additional alloying elements for increased hardenability and improved properties.
TOOL STEEL
Tool steel combines selected alloy steel and carbon steel grades, and its high hardness and abrasion resistance characteristics make it ideal for cutting and machining various types of metals.
Carbon, Alloy & Tool Steel Inventory
Scot Forge holds an inventory of various grades for customers to order for their carbon alloy and tool steel forging needs and specifications:
1010 | 1050 | 17 CrNiMo6 | 4320 | 9310 | A182F12 | MIL-S 23284CL1 |
1018 | 1055 | 2317 | 4330 | 52100 | A182F22 | MIL-S 23284CL2 |
1020 | 1060 | 3310 | 4340 | ABS Grade 2 | A 182F91 | NITRALLOY "N" |
1021 | 1065 | 4130 | 4350 | EX55 | A336F1 | NITRALLOY 135 |
1022 | 1070 | 4130API | 4620 | HY80 | A336F22A | D-2 |
1026 | 1080 | 4140 | 4820 | HY100 | A350LF2 | H-13 |
1029 | 1117 | 4142 | 6150 | A 105 | A350LF3 | L-6 |
1030 | 1141 | 4145 | 8620 | A182FI | A508CL2 | |
1035 | 1146 | 4150 | 8622 | A182F5 | A508CL3 | |
1040 | 1541V | 4150 RES. | 8630 | A182F9 | A723GR2 | |
1045 | 15B22 | 43B17 | 8822 | A182F11 | A723GR3 |
Forged Carbon, Alloy & Tool Steel Characteristics
carbon Steel
The hardenability of carbon steel is limited because only carbon is used in the material. Many grades of carbon steel are hardenable through heat treatment that includes quenching and tempering steps; however, the super high strength of stainless steels cannot be achieved with carbon steel.
Alloy Steel
Adding alloying elements - Manganese, chromium, nickel and molybdenum are some of the elements used for increased strength, toughness and wear resistance compared to carbon steel. Other desirable characteristics such as corrosion resistance, strength at elevated temperature and creep resistance are also achieved through alloying element additions.
Tool Steel
Major alloying elements in tool steel are chromium, molybdenum, vanadium and tungsten. These carbide formers allow tool steel to resist deformation and maintain a sharp cutting edge at high temperatures.
Quality Assurance
Scot Forge is proud to be ISO 9001:2015 and AS9100D certified, and our team is committed to providing outstanding customer satisfaction. Further pursuance of aerospace products has led to NADCAP accreditation in both Heat Treatment for nickel material and Nondestructive Testing.
Every Scot Forge customer gets placed with a qualified team that will guide each nickel forging delivered from the inquiry stage to order placement, expediting and shipping.
Forged Copper Advantages
Due to its heat and electrical conductivity, forged copper products are ideal for applications that serve in the Aerospace, R & D, Marine and Naval industries. Copper forgings perform well in these industries because of the combination of properties copper provides.
The Aerospace industry prefers copper forgings for its thermal and electrical characteristics and abrasion resistance. The Marine and Naval industries benefit from copper’s resistance to seawater corrosion and intrinsic biofouling properties.
Copper Mechanical Properties
Some pure copper grades exhibit very high thermal and electrical conductivity but have low strength
Other grades are able to obtain higher strengths at the loss of come conductivity
Copper has good biofouling resistance
Copper retains mechanical and electrical properties at cryogenic temperatures
Forged Copper Benefits
Electrical Conductivity
Thermal Conductivity
Ease of Forming
Nonmagnetic
Nonsparking
High Machinability
Flexibility
Copper Alloy Inventory
From creating rings, discs and blanks, to complex forged shapes, our metal forging technology creates forged copper products that exceed customer expectations. We forge to meet customer specifications and have experience forging to these common standards: ASTM B150, ASTM B170, MIL-C-15726, MIL-C-24679.
Scot Forge holds an inventory of various grades for customers to order for their copper forging needs and specifications:
C00000 | C63000 |
C10100 | C63200 |
C18000 | C71500 |
C18150 | C72420 |
C18200 | ZC-1 ™ (Chrome Zirconium Copper) |
Forged Copper Products
-
Rocket Engine Nozzle / Skirt
-
Combustion Chamber / Rocket Engine Liner
-
Lox Domes
-
Pressure Vessels
-
Copper Casting Wheels
Forged Copper Capabilities
In addition, we provide value-added processes such as saw cutting, heat treating, contour torch cutting, destructive testing, metallurgical analysis and Level III nondestructive testing for all copper forging. We ensure to deliver a finished product that is ready to be installed.
Quality Assurance
Scot Forge is proud to be ISO 9001:2015 and AS9100D certified, and our team is committed to providing outstanding customer satisfaction. Further pursuance of aerospace products has led to NADCAP accreditation in both Heat Treatment for nickel material and Nondestructive Testing.
Every Scot Forge customer gets placed with a qualified team that will guide each nickel forging delivered from the inquiry stage to order placement, expediting and shipping.
Forged Titanium Advantages
Forged titanium’s anti-corrosive properties make it an exceptional choice for marine, off-shore and saltwater environments. Titanium forgings are also well suited for applications in the Aerospace, Defense and Industrial industries as they are capable to withstand intense environmental conditions.
Products often assembled using titanium forgings include:
Aircraft, helicopters and rockets
Submarines and ships
Pressure vessels
Heat exchangers
Benefits of Forged Titanium
Highest Strength to density ration of any metallic element
Corrosion-resistant in seawater
Forged Nickel Alloys Advantages
Because of its high tolerance, forged nickel alloys are ideal applications for a variety of industries such as Aerospace, Oil & Gas, Defense and Marine. Products that can be manufactured using nickel alloys include:
Aircraft and jet engines
Rocket components
Down hole oil and gas pipeline
Off-shore/sea applications
Forged Aluminum Alloy Advantages
Because of its strength, aluminum forgings remain ideal for applications where performance and safety are a high priority as it can endure intense conditions for a wide variety of industries, including Aerospace, Semiconductor, Defense and Marine.
Benefits of Forged Aluminum
Strength to weight ratio
Light weight/low density
Corrosion resistance
High thermal conductivity
Design flexibility
Good surface finish
Fracture toughness
Fatigue and fatigue crack growth
Cryogenic properties
Stainless Steel Inventory
At Scot Forge, we produce forged stainless steel parts to meet customer requirements and specifications, with on-hand stainless steel grade types that are most commonly worked to in ASTM specs; specifically: ASTM A182, ASTM A565, ASTM A965 and ASTM A750.
Scot Forge holds an inventory of various stainless steel alloys for our customers’ stainless steel forging needs and specifications:
304/304L | 347 | 431 | 15-5PH | FERRALIUM 255 ® |
310 | 405 | 440A | 17-4PH | FERRALIUM SD40 ® |
316/316L | 410 | 440C | 254 SMO ® | |
317/317L | 416 | A182F51/DUPLEX 2205 | NITRONIC GRADES | |
321 | 420 | 13-8PH |
Quality Assurance
Scot Forge is proud to be ISO 9001:2015 and AS9100D certified, and our team is committed to providing outstanding customer satisfaction. Further pursuance of aerospace products has led to NADCAP accreditation in both Heat Treatment for nickel material and Nondestructive Testing.
Every Scot Forge customer gets placed with a qualified team that will guide each nickel forging delivered from the inquiry stage to order placement, expediting and shipping.
On-Hand Nickel-Based Material
Scot Forge can forge nickel alloys to your specific requirements and specifications. From creating rings, discs and blanks to complex forged shapes, our metal forging technology creates forged nickel products that exceed customer expectations.
Scot Forge holds an inventory of various alloys for customers to order for their nickel forging needs and specifications:
Commercially Pure (CP) | Inconel 686 (UNS N06686) | Incoloy 800H (UNS N08810) |
Monel 400 (UNS N04400) | Inconel 716 (UNS N07716) | Incoloy 800HT (UNS N08811) |
Monel K500 (UNS N05500) | Inconel 718 (UNS N07718) | Incoloy 825 (UNS N08825) |
Inconel 600 (UNS N06600) | Inconel 725 (UNS NO7718) | Hastelloy C276 (UNS N10276) |
Inconel 617 (UNS N06617) | Inconel X750 (UNS N07750) | |
Inconel 625 (UNS N06625) | Incoloy 020 (UNS N08020) |
Forged Nickel Alloy Advantages
Because of their high tolerance, forged nickel alloys are ideal applications for various industries such as Aerospace, Oil & Gas, Defense and Marine.
Inconel
Inconel is a family of nickel-chromium-based superalloys that exhibit excellent strength, corrosion resistance, and high-temperature capabilities.
Benefits of inconel
a. High-Temperature Resistance: Inconel alloys retain their strength and mechanical properties at elevated temperatures, making them ideal for applications in gas turbines, aerospace, and petrochemical industries.
b. Corrosion Resistance: Inconel offers exceptional resistance to corrosion, including oxidation, reducing environments, and corrosive media like acids and salts, making it suitable for marine and chemical processing applications.
c. Excellent Mechanical Properties: Inconel alloys possess superior mechanical properties, such as high tensile and fatigue strength, which ensure their reliability in demanding conditions.
d. Weldability: Inconel exhibits good weldability, allowing for easy fabrication and repair of components.
APplications
a. Aerospace and Defense: Inconel is widely used in aircraft engines, gas turbine blades, exhaust systems, and heat shields due to its ability to withstand high temperatures and mechanical stress.
b. Petrochemical and Chemical Processing: Inconel resists corrosion and stress cracking in aggressive environments, making it suitable for applications like heat exchangers, reactors, and piping systems.
c. Oil and Gas: Inconel is used in downhole tools, valves, and wellhead components due to its resistance to high-pressure and corrosive conditions.
d. Nuclear Power: Inconel alloys are employed in reactor cores, steam generators, and other critical components due to their resistance to radiation and high-temperature environments.
Monel
Monel is a group of nickel-copper alloys known for their excellent corrosion resistance, especially in marine and chemical environments.
Benefits of monel
a. Corrosion Resistance: Monel alloys exhibit exceptional resistance to various corrosive media, including seawater, acids, alkalis, and industrial gases.
b. High Strength: Monel alloys possess good mechanical strength, making them suitable for high stress and pressure applications.
c. Heat Resistance: Monel maintains its mechanical properties and corrosion resistance at elevated temperatures, making it suitable for high-temperature applications.
Applications
a. Marine and Offshore: Monel is extensively used in marine applications such as propeller shafts, pump shafts, valves, and fasteners due to its resistance to seawater corrosion.
b. Chemical Processing: Monel is utilized in equipment like heat exchangers, valves, and pumps in the chemical industry due to its resistance to various corrosive chemicals.
c. Oil and Gas: Monel alloys are used in oil refineries, offshore platforms, and pipelines due to their resistance to corrosive environments and high-pressure conditions.
Incoloy
Incoloy is a group of nickel-based alloys renowned for their excellent high-temperature strength and corrosion resistance.
Benefits of incoloy
a. High-Temperature Strength: Incoloy alloys offer remarkable strength and stability at elevated temperatures, making them suitable for furnace components, heat-treating equipment, and power generation systems.
b. Corrosion Resistance: Incoloy exhibits excellent resistance to oxidation and corrosion, making it ideal for applications in chemical processing, pollution control, and marine environments.
c. Thermal Stability: Incoloy alloys retain their mechanical properties over various temperatures, including cryogenic environments.
Applications
a. Power Generation: Incoloy is extensively used in gas turbines, heat exchangers, and boiler components due to its high-temperature strength and corrosion resistance.
b. Chemical Processing: Incoloy alloys find applications in reactors, pipelines, and heat exchangers due to their resistance to aggressive chemicals and high-temperature environments.
c. Aerospace: Incoloy is employed in components like jet engines, exhaust systems, and combustion chambers due to its ability to withstand high temperatures and corrosive gases.
Forged Stainless Steel Applications
Forged stainless steel is popularly used in a variety of industries, such as Industrial, Food, Infrastructure and Oil & Gas due to its ability to perform in high stress and corrosive environments. Parts that can be manufactured using stainless steel forging include:
-
Construction and Infrastructure: Stainless steel is utilized in buildings, bridges, tunnels, and other infrastructure projects due to its strength, corrosion resistance, and architectural appeal.
-
Oil and Gas: Stainless steel is employed in pipelines, storage tanks, and refineries due to its resistance to corrosive substances and high-temperature environments.
-
Energy and Power Generation: Stainless steel is used in power plants, nuclear facilities, nuclear waste container vessels and renewable energy sectors for applications such as turbine blades and shafts, heat exchangers and exhaust systems.
-
Transportation: Stainless steel is utilized in automobiles, trains, aircraft, and ships for various components, including exhaust systems, structural parts and interior fittings.
-
Medical and Healthcare: Stainless steel is commonly used in medical equipment, structural components for cryogenic vessels, surgical instruments, implants and hospital infrastructure due to its hygienic properties and biocompatibility.
-
High strength parts for saltwater environments
-
17-4PH forged bar
Forged Stainless Steel Grades & Characteristics
Stainless steel has overall benefits of corrosion resistance and machinability, and each grade type of stainless steel comes with its own set of benefits:
Austenitic Stainless steel
-
Highest impact strength
-
Cryogenic toughness
-
Non-magnetic
MARTENSITIC STAINLESS STEEL
-
High strength
-
Pitting corrosion resistance
PRECIPITATION HARDENING (PH) STAINLESS STEEL
-
Extreme strength and fatigue life
-
Moderate toughness
DUPLEX STAINLESS STEEL
-
Sound combination of strength and corrosion resistance
-
Reliable toughness at room temperature
Benefits of Stainless Steel
Stainless steel offers a range of benefits that make it a preferred material across different sectors.
Corrosion Resistance: Stainless steel is renowned for its exceptional corrosion resistance, making it highly resistant to rust, stains, and environmental factors. It contains chromium, which forms a protective oxide layer on the surface, providing resistance to various corrosive media, including acids, alkalis, and moisture. This property is particularly valuable in industries such as:
-
Marine and Offshore: Stainless steel is extensively used in shipbuilding, offshore platforms, and coastal structures due to its ability to withstand the harsh conditions of seawater.
-
Chemical Processing: The resistance of stainless steel to corrosive chemicals makes it suitable for equipment like tanks, pipelines, and valves used in chemical plants.
-
Food and Beverage: Stainless steel is commonly utilized in the food and beverage industry due to its hygienic properties, ease of cleaning, and resistance to food acids and contamination.
Strength and Durability: Stainless steel exhibits excellent mechanical properties, including high strength, toughness, and durability. It maintains its integrity even at extreme temperatures, making it ideal for various applications, such as:
-
Construction and Architecture: Stainless steel is used in structural components, building facades, roofing, and bridges due to its strength, aesthetic appeal, and resistance to weathering.
-
Automotive: Stainless steel finds application in exhaust systems, automotive frames, and body components due to its strength, heat resistance, and corrosion resistance.
-
Medical and Pharmaceutical: Stainless steel is widely used in medical instruments, surgical equipment, and implantable devices due to its biocompatibility, sterilizability and corrosion resistance.
-
Hygiene and Cleanability: Stainless steel possesses a smooth and non-porous surface, making it easy to clean and maintain hygiene standards and highly suitable for industries with stringent cleanliness requirements, including:
-
Pharmaceutical: Stainless steel is used in pharmaceutical equipment, storage tanks, and cleanroom environments due to its ease of cleaning and resistance to contamination.
-
Food Processing: Stainless steel is employed in food processing equipment, storage containers, and kitchen appliances due to its non-reactive nature, ease of cleaning, and corrosion resistance.
Forged Nickel Inventory
Scot Forge can forge nickel alloys to your specific requirements and specifications. From creating rings, discs and blanks, to complex forged shapes, our metal forging technology creates forged nickel products that exceed customer expectations.
Scot Forge holds an inventory of various alloys for customers to order for their nickel forging needs and specifications:
Inconel 625 (UNS N06625) | Incoloy 020 (UNS N08020) | |
Inconel 617 (UNS N06617) | Inconel X750 (UNS N07750) | |
Inconel 600 (UNS N06600) | Inconel 725 (UNS NO7718) | Hastelloy C276 (UNS N10276) |
Monel K500 (UNS N05500) | Inconel 718 (UNS N07718) | Incoloy 825 (UNS N08825) |
Monel 400 (UNS N04400) | Inconel 716 (UNS N07716) | Incoloy 800HT (UNS N08811) |
Commercially Pure (CP) | Inconel 686 (UNS N06686) | Incoloy 800H (UNS N08810) |
Quality Assurance
Scot Forge is proud to be ISO 9001:2015 and AS9100D certified, and our team is committed to providing outstanding customer satisfaction. Further pursuance of aerospace products has led to NADCAP accreditation in both Heat Treatment for nickel material and Nondestructive Testing.
Every Scot Forge customer gets placed with a qualified team that will guide each nickel forging delivered from the inquiry stage to order placement, expediting and shipping.
Forged Titanium Inventory
While Scot Forge typically produces forged titanium products to meet customer requirements and specifications, we also offer titanium forging services to these common industry standards: ASTM B381, AMS4928, AMS4931, AMS6931, SAE AMS4921, MIL-T-9047.
Scot Forge holds an inventory of various alloys for customers to order for their titanium forging needs and specifications:
Commercially Pure (CP) | Ti-6Al-4V |
Gr. 2, Gr. 3, Gr. 4 | Ti-6Al-4V Extra Low Interstitial |
Quality Assurance
Scot Forge is proud to be ISO 9001:2015 and AS9100D certified, and our team is committed to providing outstanding customer satisfaction. Further pursuance of aerospace products has led to NADCAP accreditation in both Heat Treatment for nickel material and Nondestructive Testing.
Every Scot Forge customer gets placed with a qualified team that will guide each nickel forging delivered from the inquiry stage to order placement, expediting and shipping.
Aluminum Inventory
Scot Forge forges aluminum to meet customer specifications, Scot Forge also offers aluminum forgings in the following common alloys:
1100 | 2618 | 5083 | 6061 | 7079 |
2014 | 3003 | 5086 | 7039 | 7175 |
2024 | 4032 | 5383 | 7050 | Highlander 613 ™ |
2219 | 5052 | 5456 | 7075 |
Highly-Skilled Partner
Scot Forge metallurgists, forge engineers and sales engineers can partner with your team to give advice on the following manufacturing practices for proprietary aluminum work:
-
Thermal Mechanical Processing (TMP)
-
Microstructural and grain size control
-
Engineered micro and macro-structures to meet the specific service conditions and direction of loading
-
Forging and thermal practices
-
Stress-relieving for optimal machining and stress corrosion cracking resistance
Quality Assurance
Scot Forge is proud to be ISO 9001:2015 and AS9100D certified, and our team is committed to providing outstanding customer satisfaction. Further pursuance of aerospace products has led to NADCAP accreditation in both Heat Treatment for nickel material and Nondestructive Testing.
Every Scot Forge customer gets placed with a qualified team that will guide each nickel forging delivered from the inquiry stage to order placement, expediting and shipping.
Questions? Contact a forging expert
Forged Carbon, Alloy & Tool Steel Advantages
Low Carbon Steel
Low carbon steel has 0.05% to 0.25% carbon which allows the material to be ductile. Low carbon steel is a low-cost option for applications where high strength is not a consideration.
Medium Carbon Steel
Medium carbon steel has 0.29% to 0.54% carbon which contains a higher amount of manganese and allows the material to be quenched and tempered after forging. These forgings offer higher strength and toughness than low carbon steels, yet avoid the higher costs associated with the highly alloyed stainless steels.
High and Very High Carbon Steel
High and very high carbon steel has 0.55% to 2.1% carbon which allows the material to achieve high hardness and resilience.
Carbon steel hardened by heat treatment has increased strength and toughness. Tool steels, containing higher amounts of carbon, are normally forged for the purpose of creating tools that can resist abrasion, fatigue and wear.
Benefits Of Forged Carbon, Alloy & Tool Steel
Benefits of Carbon Steel:
-
Strength and Durability: Carbon steel offers excellent tensile strength and hardness, making it suitable for structural components and machinery parts that require high strength and resistance to wear.
-
Cost-Effectiveness: Carbon steel is comparatively less expensive than other steel types, making it an economical choice for various applications.
-
Machinability: Carbon steel is easy to machine and fabricate, allowing for efficient production of components with intricate shapes.
Benefits of Alloy Steel:
-
Enhanced Strength and Toughness: Alloying elements improve the strength, hardness, and toughness of steel, enabling its use in demanding applications that require resistance to high-temperature environments, pressure, and mechanical stress.
-
Corrosion Resistance: Certain alloy steels exhibit improved corrosion resistance, making them suitable for applications in aggressive environments.
-
Wear Resistance: Alloy steels can possess excellent wear resistance, ensuring their longevity and suitability for applications involving friction and abrasive forces.
Benefits of Tool Steel:
-
High Hardness and Wear Resistance: Tool steel possesses excellent hardness, allowing it to withstand high cutting forces and resist wear during machining processes.
-
Toughness and Shock Resistance: Tool steel exhibits high toughness, enabling it to absorb shock and resist deformation, making it suitable for applications involving high impact and repetitive stresses.
-
Heat Resistance: Tool steel retains its hardness and toughness even at high temperatures, allowing it to withstand the thermal stresses associated with high-speed machining and heat treatment processes.
Carbon, Alloy & Tool Steel Applications
Carbon Steel:
-
Construction: Carbon steel is widely used in construction for structural frameworks, bridges, and reinforcement bars due to its high strength and durability.
-
Automotive: Carbon steel is employed in automobile frames, chassis components, and suspension systems due to its strength, impact resistance, and affordability.
-
Infrastructure: Carbon steel is utilized in pipelines, tanks, and machinery for various industrial applications, including oil and gas, water treatment, and manufacturing.
Alloy Steel
-
Aerospace and Defense: Alloy steel is used in aircraft components, landing gear, and structural parts due to its high strength, fatigue resistance, and temperature stability.
-
Oil and Gas: Alloy steel finds application in oil and gas exploration, drilling, and production equipment due to its resistance to corrosion, high pressure, and harsh operating conditions.
-
Automotive and Transportation: Alloy steel is employed in engine components, gears, axles, and suspension systems in the automotive and transportation industries due to its strength, durability, and heat resistance.
Tool Steel
-
Manufacturing: Tool steel is used in the manufacturing industry for the production of cutting tools, dies, molds, and machine components that require high hardness and wear resistance.
-
Automotive: Tool steel finds application in the automotive industry for the production of forging dies, punches, and cutting tools used in metal forming and machining processes.
-
Plastics and Injection Molding: Tool steel is utilized in the plastics industry for the production of molds and dies used in injection molding, extrusion, and blow molding processes.
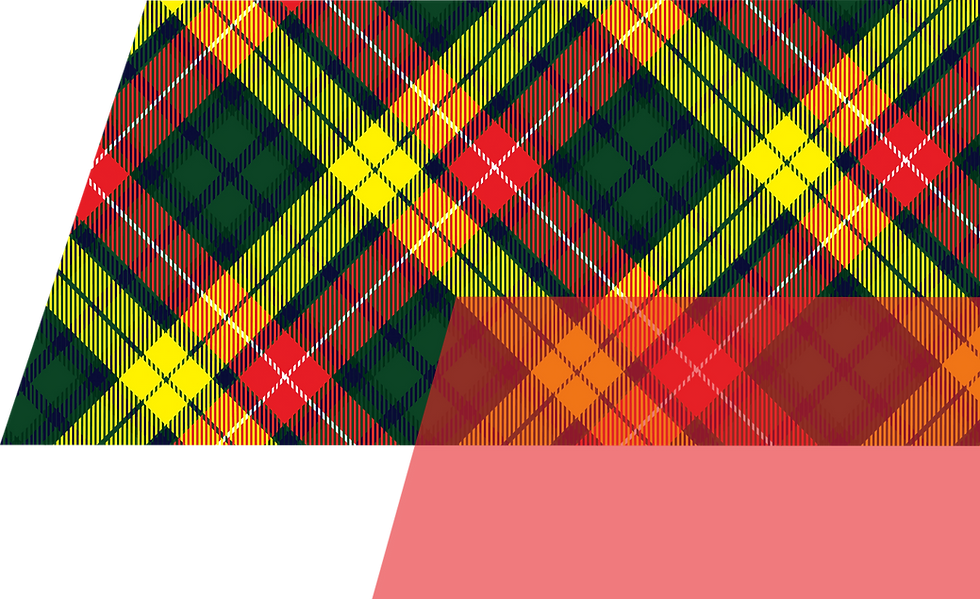
Scot Forge Difference
At Scot Forge, we know the importance of getting your parts on-time, as expected. However, for customers new to procuring forgings, ordering a forging that will meet all specifications for end-use applications may be a challenge, which is why finding a trusted supplier and partner is essential. Our employee-owners are here to ensure your project stays on track with our forgings by offering:
We offer many size forgings in both standard and unique geometries to meet your needs.
Pro Tip - Did you know near-net shapes can save you time and money? Oftentimes, a customer calls to order a disc, which they will later machine down to a more shaped part. By working with our technically trained sales team, you can get your finished product shape as close as possible to optimize your production process.
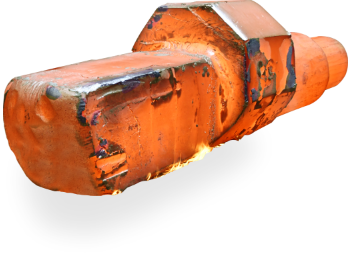
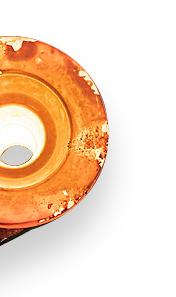
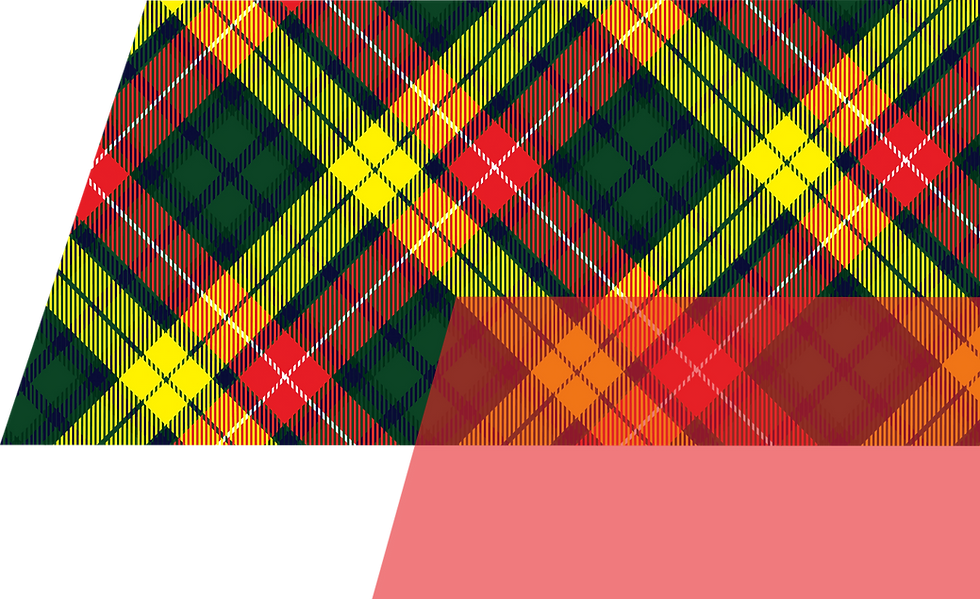