
Forge Consultation & Custom Engineering
.jpg)
Forge Consultation & Engineering
Our Forge Engineering team brings more than 90 years of combined experience to your project, which includes first-hand blacksmithing and modern forge simulation technology. They have developed a unique semi-closed die forging technique that allows for the flexibility of open die forging with the near-net shape of closed die. This method allows the conversion of pieces from castings or fabrications to forging that were once thought not possible or cost-effective.
.jpg)
Forge Consultation & Engineering
Our Forge Engineering team brings more than 90 years of combined experience to your project, which includes first-hand blacksmithing and modern forge simulation technology. They have developed a unique semi-closed die forging technique that allows for the flexibility of open die forging with the near-net shape of closed die. This method allows the conversion of pieces from castings or fabrications to forging that were once thought not possible or cost-effective.
Reducing manufacturing costs. Improving part performance. Minimizing material waste
The Scot Forge customer value engineering team brings the knowledge of custom forging experts to work in your plant, helping you to achieve long-term cost reductions, enhanced part performance and improved lead times through:
Near-net shape parts not previously available
Component reduction - weldment elimination
Optimizing your specifications and manufacturing practices
Computer simulations to design parts to take advantage of forged properties
Customizing alloy development and thermal treatments for your application
Optimizing your specifications and manufacturing practices
Reducing manufacturing costs. Improving part performance. Minimizing material waste
The Scot Forge customer value engineering team brings the knowledge of custom forging experts to work in your plant, helping you to achieve long-term cost reductions, enhanced part performance and improved lead times through:
Near-net shape parts not previously available
Component reduction - weldment elimination
Optimizing your specifications and manufacturing practices
Computer simulations to design parts to take advantage of forged properties
Customizing alloy development and thermal treatments for your application
Optimizing your specifications and manufacturing practices
Optimized Specifications
Our technically trained Account Managers, Forge Development team and Metallurgists can increase your product value with customized solutions that meet your existing requirements. Even the simplest material change or process modification has helped many Scot Forge customers realize significant savings.
How we deliver added value for our customers:
Improve lead times
Lower part costs
Eliminate non-value processing
Reduce marking costs
Enhance quality
Even the simplest material change or process modification has helped many Scot Forge customers realize significant savings. Below are just a few examples.
Optimized Specifications
Our technically trained Account Managers, Forge Development team and Metallurgists can increase your product value with customized solutions that meet your existing requirements. Even the simplest material change or process modification has helped many Scot Forge customers realize significant savings.
How we deliver added value for our customers:
Improve lead times
Lower part costs
Eliminate non-value processing
Reduce marking costs
Enhance quality
Even the simplest material change or process modification has helped many Scot Forge customers realize significant savings. Below are just a few examples.
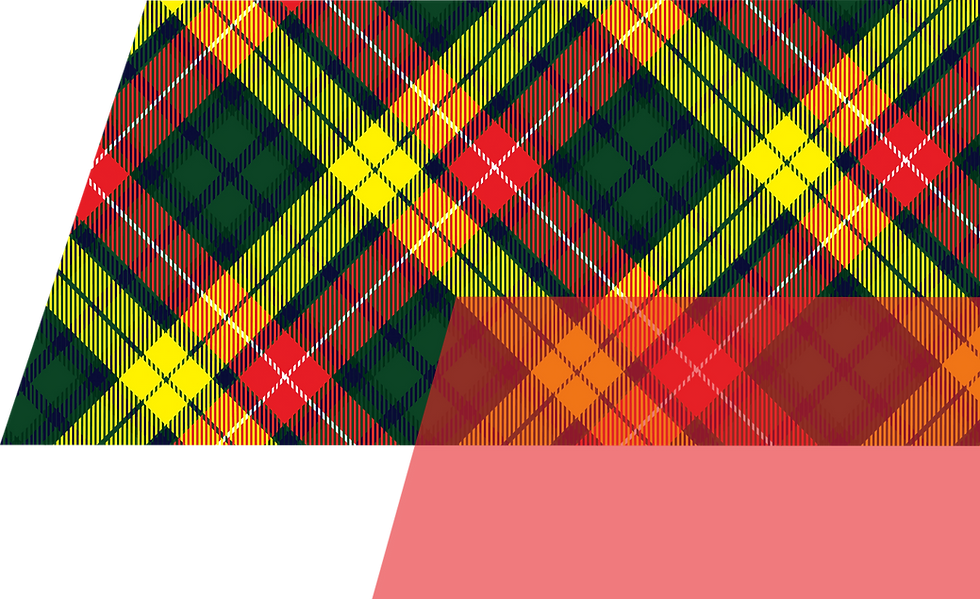
Computer Modeling & Simulation
Our Forge Engineering team has a full range of simulation capabilities to test and validate material shaping, which will enable more precise tool design and optimal forge process plans. As a result, material and machining requirements are reduced, minimizing costs and turnaround times.


Our accurate simulations model a wide range of metalworking and material characteristics including:
-
Complex shapes
-
Upsetting
-
Forward extrusion
-
Back extrusion
-
Gear forming
-
Stress analysis
-
Heat treat modeling
-
Grain flow characteristics
As an extension of your team we provide unmatched technical expertise, discover what we can add to your project in the download below.
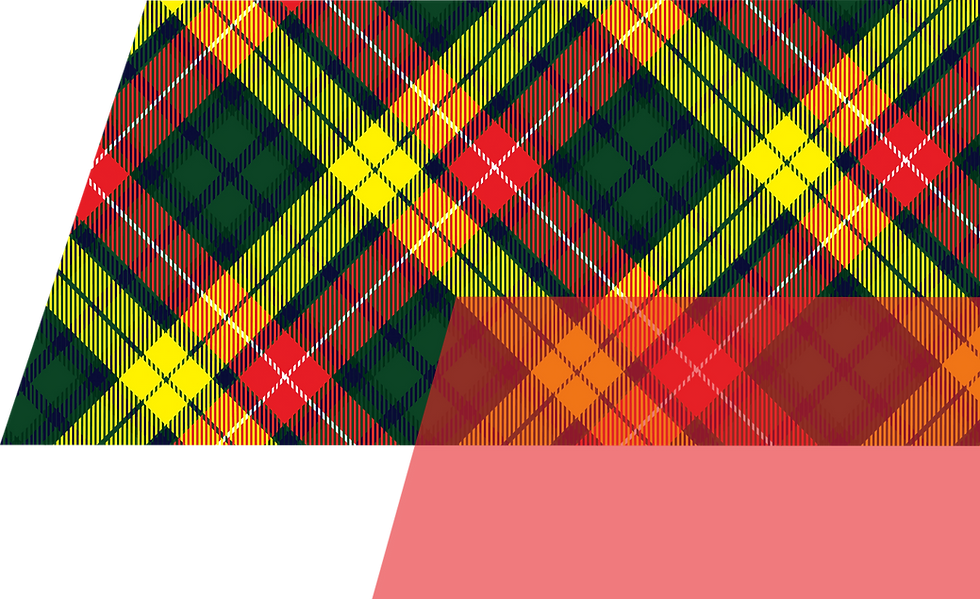
Computer Modeling & Simulation
Our Forge Engineering team has a full range of simulation capabilities to test and validate material shaping, which will enable more precise tool design and optimal forge process plans. As a result, material and machining requirements are reduced, minimizing costs and turnaround times.


Our accurate simulations model a wide range of metalworking and material characteristics including:
-
Complex shapes
-
Upsetting
-
Forward extrusion
-
Back extrusion
-
Gear forming
-
Stress analysis
-
Heat treat modeling
-
Grain flow characteristics
As an extension of your team we provide unmatched technical expertise, discover what we can add to your project in the download below.
Product specification type
Thermal Treatment

Previous problems
-
Past practices on a customer part called for normalizing, quenching and double tempering. These practices ran up costs and production times.
-
Previous requirements on a customer application called for meeting both a minimum tempering temperature and a hardness range on certain parts. This often resulted in a requenching operation, which lengthened lead times.

Modified solution
-
By eliminating the normalizing and second tempering operations which were unnecessary, the customer saved over 7¢ per pound, as well as one to two weeks' lead time.
-
Through temperature modification, not only was Scot Forge able to meet the specification the first time, but also shorten the lead time.
Product specification type
Material Grade

PREVIOUS PROBLEMS
-
A customer was looking for cost reduction assistance with a gear application which needed to meet Brinell requirements and was formerly specified as 4340 material.
-
The customer was previously specifying Vacuum Arc Remelting (VAR) material for a pinion shaft. Lead times were unacceptably long, and the material costs were extremely high.

MODIFIED SOLUTION
-
The substitution of 4150 for 4340 lowered part costs by 10%, while still meeting minimum Brinell requirements.
-
By switching from VAR material to air melt, lead times were reduced by months, and base material costs were reduced by over 45% without sacrificing product quality.
Product specification type
Marking/Stamping

Previous problems
-
Previous requirements on a customer application called for meeting both a minimum tempering temperature and a hardness range on certain parts. This often resulted in a requenching operation, which lengthened lead times.

Modified solution
-
Now a simple purchase order and heat number identify each part, saving time and excess marking costs.
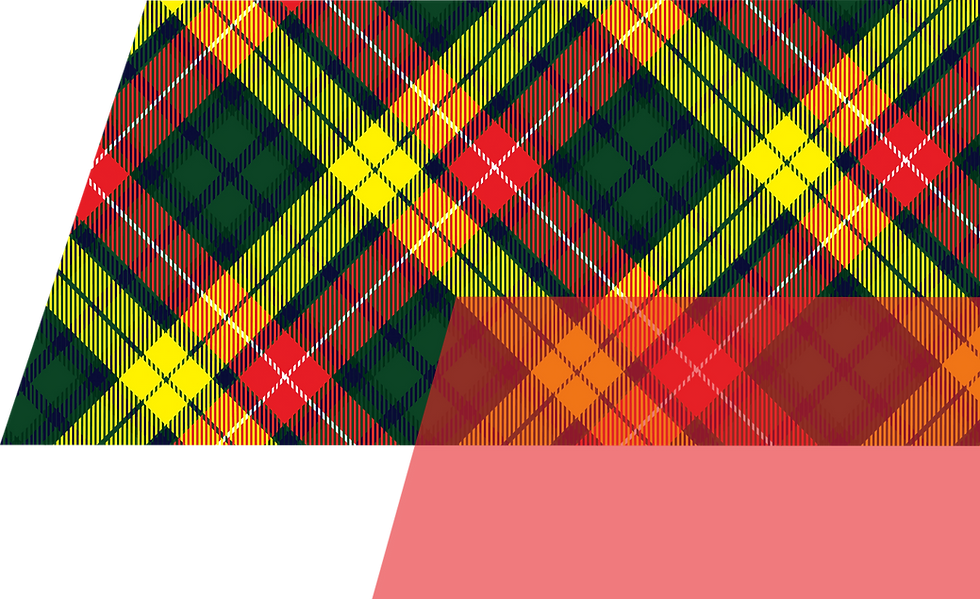
Scot Forge Difference
At Scot Forge, we know the importance of getting your parts on-time, as expected. However, for customers new to procuring forgings, ordering a forging that will meet all specifications for end-use applications may be a challenge, which is why finding a trusted supplier and partner is essential. Our employee-owners are here to ensure your project stays on track with our forgings by offering:
Quality Assurance
Scot Forge is proud to be ISO 9001:2015 and AS9100D certified, and our team is committed to providing outstanding customer satisfaction. Further pursuance of aerospace products has led to NADCAP accreditation in both Heat Treatment for nickel material and Nondestructive Testing.
Every Scot Forge customer gets placed with a qualified team that will guide each nickel forging delivered from the inquiry stage to order placement, expediting and shipping.
We offer many size forgings in both standard and unique geometries to meet your needs.
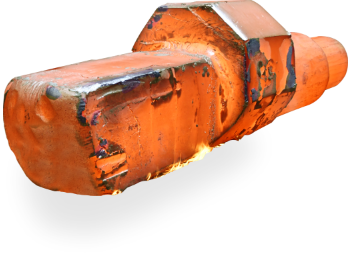
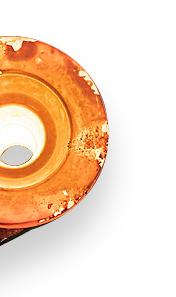