
PRESSURE VESSEL EQUIPMENT FORGINGS
.jpg)
Why Forged ASME Pressure Vessels Components?
Pressure vessels are integral to many manufacturing facilities and processing plants, from industrial boilers to gasoline tankers. Pressure vessels operate in potentially hazardous environments and safely store pressurized liquids and gases. However, pressure vessels can be dangerous if not correctly designed, manufactured and maintained.
At Scot Forge, we understand the critical nature of your parts. We know that failure is not an option, which is why we strive to act as an extension of your team to find the most effective, cost-efficient manufacturing methods to get you forgings you can rely on, on time. As a result, our pressure vessels components can be found in gas plants, refineries, power plants, chemical plants, space launch facilities, offshore platforms and numerous industrial applications.
Forging for ASME Boiler Pressure Vessel Code
A pressure vessel is fabricated, requiring forging, rolling and welding metal. If your team requires the integrity of forgings and needs a true partner specializing in one-piece shapes such as spheres, cylinders, cones and more, the Scot Forge employee-owners are here to help. We have the industry experts in-house, from forge engineers to metallurgists, who even help write the ASME (American Society of Mechanical Engineers) industry standards for forgings. These ASME experts on staff ensure your pressure vessels meet ASME BPVC (Boiler Pressure Vessel Code) Section VIII from material cleanliness to final inspection.
ASME BPVC Section VIII Division 1 for a design-by-rule approach
ASME BPVC Section VIII Division 2 for a design-by-analysis approach.
ASME BPVC Section VIII Division 3 for pressure vessels that require internal or external operating at a pressure above 10,000 PSI.
To meet the requirements specified on your purchase agreement and ensure the reliability of your pressure vessel components, we offer ultrasonic testing, magnetic particle testing and liquid penetrant testing and, if needed, destructive testing options.
Common Pressure Vessel ASME Specifications
A266/A266M - Carbon Steel Forgings for Pressure Vessel Components
A288 -Carbon and Alloy Steel Forgings for Magnetic Retaining Rings for Turbine Generators
A372/A372M - Carbon and Alloy Steel Forgings for Thin-Walled Pressure Vessels
A541/A541M - Quenched and Tempered Carbon and Alloy Steel Forgings for Pressure Vessel Components
A765/A765M - Carbon Steel and Low-Alloy Steel Pressure-Vessel-Component Forgings with Mandatory Toughness Requirements
A859/A859M - Age-Hardening Alloy Steel Forgings for Pressure Vessel Components
A1049/A1049M - Stainless Steel Forgings, Ferritic/Austenitic (Duplex), for Pressure Vessels and Related Components
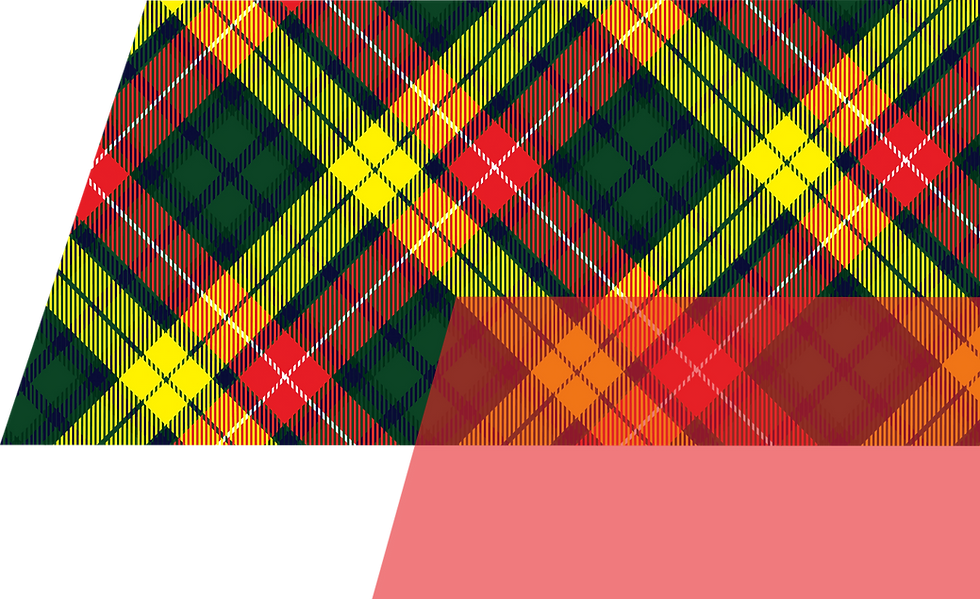
Types of Pressure Vessels
Pressure vessels are enclosed containers that hold or store liquids, vapors or gases under pressure significantly higher or lower than the pressure outside the container. Many pressure vessels are in use worldwide, but the three most common are storage vessels, heat exchangers and process vessels.
Process Vessels
Process vessels work to accomplish a task such as separation, heating, cooling, purification, blending and more. These versatile pressure vessels are often part of a production process line, where different tanks are used together to process a product.
Types of Pressure Vessels
Cylindrical Pressure Vessels
Spherical Pressure Vessels
Horizontal Pressure Vessels
Vertical Pressure Vessels
Heat Exchangers
Heat exchangers enable the exchange of energy through heat without direct contact. For example, heat exchangers are often used to salvage heat from waste gases in waste processing facilities. Generally, this system contains a series of metal tubes, where one product flows through these tubes while a second product flows around the tubes, transferring heat from one product to another.
Storage Vessels
Many products require pressure to be stored appropriately, including propane, ammonia, butane, chlorine and LPG and storage pressure vessels are uniquely designed to accommodate each specific product type and temperature.
Reasons to Choose Scot Forge
Scot Forge has material for pressure vessels on the floor, ready to forge into the parts your design calls for, such as shells, cones (reducers), repads, skids, saddle supports, base rings, internals and more. Helping you create production equipment, compression equipment, separators, reactors, dehydrators, scrubbers and towers.
Forging Capabilities Combined with Value Engineering
We can develop near-net shaped solutions to meet your drawing requirements. Our vast forging capabilities enable us to reduce forged section sizes and improve mechanical properties.
Fast Quotes and Personalized Service
We understand your need for a supplier with expert knowledge of your industry and your specific component requirements. Our knowledgeable technical sales team is ready to consult with you and provide fast quotes based on your needs. We strive to assist you in meeting your design challenges and program objectives with clear communications from order status to milestone achievements.
On-time Delivery
During a rebuild, you never know what you may find. We have a fully staffed department dedicated to tracking and maintaining high on-time delivery performance. In crucial circumstances, reduced lead times can be offered for breakdown and emergency orders in need of immediate production response to get items out of the critical path.
Questions? Contact a Forging Expert
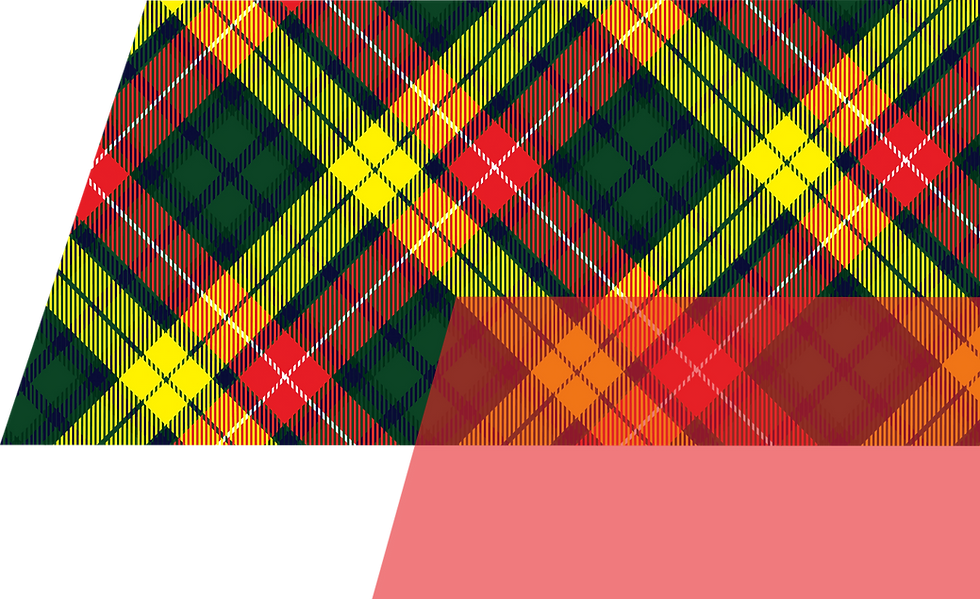
Scot Forge Difference
At Scot Forge, we know the importance of getting your parts on-time, as expected. However, for customers new to procuring forgings, ordering a forging that will meet all specifications for end-use applications may be a challenge, which is why finding a trusted supplier and partner is essential. Our employee-owners are here to ensure your project stays on track with our forgings by offering:
We offer many size forgings in both standard and unique geometries to meet your needs.
Pro Tip - Did you know near-net shapes can save you time and money? Oftentimes, a customer calls to order a disc, which they will later machine down to a more shaped part. By working with our technically trained sales team, you can get your finished product shape as close as possible to optimize your production process.
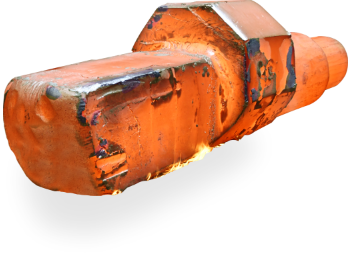
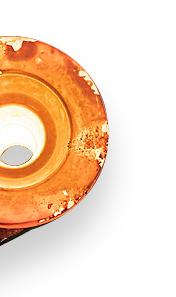